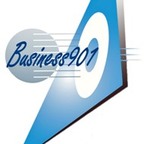
Business901
Summary: Business901 is a firm specializing in bringing the continuous improvement process to the sales and marketing arena. Joe Dager, owner of Business901 takes his process thinking of over thirty years in marketing within a wide variety of industries and applies it through Lean Marketing Concepts. Are you marketing to the unprofitable masses? Marketing through a funnel of depletion is not only costly but ineffective. Lean Marketing establishes pull and allows you to develop and implement the Funnel of Opportunity.
- Visit Website
- RSS
- Artist: Joe Dager
- Copyright: Copyright © 2017 Joseph Dager. All rights reserved.
Podcasts:
Lean Design and Lean Construction Consultant, Trainer and Author, Alan Mossman of The Change Business says; For the same reason that we don't use a bilateral transactional contract for marriage, we use a relational contract. It's now recognized that there's much more sense in using a relational contract for these long‑term arrangements where we need to work together to get things done. Our conversation centers around The Last Planner® a project management system created by Glenn Ballard and Greg Howell co-founders of the Lean Construction Institute. In long term building projects, they have found that managing relationships is the important part of project management. Last week, I had a post that discussed this, Crucial & Collaborative Conversations for Predictable Design & Delivery and talked about it even more in this post, Is Relationship Mapping the new Critical Path?. Alan Mossman trained as an architect and worked for many years in management and organization development. He only returned to construction in 2000 building on his knowledge and understanding of collaboration, systems thinking, quality and lean. An accredited UK based Last Planner trainer, he has coached teams implementing Lean and Last Planner for a wide range of clients in Europe, Africa and Australasia. From 2004 to 2010 Alan was a founding Director of The Lean Construction Institute UK. He helped set up the Lean Construction Journal www.leanconstructionjournal.org and was co-editor from 2003 to 2012. You may be interested in the Lean Service Design Trilogy Workshop.
Lean Design and Lean Construction Consultant, Trainer and Author, Alan Mossman of The Change Business says; For the same reason that we don't use a bilateral transactional contract for marriage, we use a relational contract. It's now recognized that there's much more sense in using a relational contract for these long‑term arrangements where we need to work together to get things done. Our conversation centers around The Last Planner® a project management system created by Glenn Ballard and Greg Howell co-founders of the Lean Construction Institute. In long term building projects, they have found that managing relationships is the important part of project management. Last week, I had a post that discussed this, Crucial & Collaborative Conversations for Predictable Design & Delivery and talked about it even more in this post, Is Relationship Mapping the new Critical Path?. Alan Mossman trained as an architect and worked for many years in management and organization development. He only returned to construction in 2000 building on his knowledge and understanding of collaboration, systems thinking, quality and lean. An accredited UK based Last Planner trainer, he has coached teams implementing Lean and Last Planner for a wide range of clients in Europe, Africa and Australasia. From 2004 to 2010 Alan was a founding Director of The Lean Construction Institute UK. He helped set up the Lean Construction Journal www.leanconstructionjournal.org and was co-editor from 2003 to 2012. You may be interested in the Lean Service Design Trilogy Workshop.
Lean Design and Lean Construction Consultant, Trainer and Author, Alan Mossman of The Change Business says; For the same reason that we don't use a bilateral transactional contract for marriage, we use a relational contract. It's now recognized that there's much more sense in using a relational contract for these long‑term arrangements where we need to work together to get things done. Our conversation centers around The Last Planner® a project management system created by Glenn Ballard and Greg Howell co-founders of the Lean Construction Institute. In long term building projects, they have found that managing relationships is the important part of project management. Last week, I had a post that discussed this, Crucial & Collaborative Conversations for Predictable Design & Delivery and talked about it even more in this post, Is Relationship Mapping the new Critical Path?. Alan Mossman trained as an architect and worked for many years in management and organization development. He only returned to construction in 2000 building on his knowledge and understanding of collaboration, systems thinking, quality and lean. An accredited UK based Last Planner trainer, he has coached teams implementing Lean and Last Planner for a wide range of clients in Europe, Africa and Australasia. From 2004 to 2010 Alan was a founding Director of The Lean Construction Institute UK. He helped set up the Lean Construction Journal www.leanconstructionjournal.org and was co-editor from 2003 to 2012. You may be interested in the Lean Service Design Trilogy Workshop.
Well said by author Allan R. Coletta of a new book The Lean 3P Advantage: A Practitioner’s Guide to the Production Preparation Process. Development of the 3P process is attributed to Chichiro Nakao, a former Toyota group manager and the founder of Shingijutsu company. The accepted meaning of 3P is Production, Preparation, Process. Allan is a chemical engineer with an extensive background in manufacturing operations, supply chain and engineering, gained while working in the chemical process and healthcare diagnostics industries. Allan is a practitioner more so than an author and I believe you will enjoy that perspective. Toyota delivers product designs on schedule 98% of the time (as stated by @flowchainsensei on twitter). Now, I am not sure how I can confirm this statement except that I believe this source to be accurate and even if Bob was 50% wrong, it would mean Toyota still exceeds the majority. However, after interviewing Allan and reading the book, I can understand and believe that statement. This is an excerpt from the book: Lean 3P is a powerful enabler for invention and innovation because it creates a structure and a process for people to create both independently and collaboratively. However, 3P is not presented as a "one size fits all" means of creating brilliant new products that takes us from "blue sky" to product launch. It might work like that in some instances where a new product is a variation of an established product or in organizations where the same team is inventing, developing, and working together to launch a new product. With additional experience the role of 3P in the full product development will likely expand. For companies new to Lean 3P, the question might be how 3P will integrate into existing product development processes. A recent blog post, Applying Lean in the Lean 3P Design Process contains a written excerpt from the podcast. I talked to Allan for a rather long time and had to shorten the podcast. I chose to cut his acknowledgments of several people that include Andy Johnson, Maria Stopher, Ken Rolfes and two former Business901 podcast guests, Drew Locher and Ron Masticelli. I apologize to any that he mentioned and I failed to here. Allan’s Lean experience started while serving as Site Manager for ICI Uniqema’s largest Specialty Chemicals plant in North America and continued to expand is his role as Senior Director of Engineering for Siemens Healthcare Diagnostics. His passion for manufacturing and engaging people in continuous improvement continues to grow through personal application of Lean principles. Allan serves on the Delaware Manufacturing Extension Partnership’s Fiduciary and Advisory Boards, and is a member of the Delaware Business Mentoring Alliance. He is also a member of the American Institute of Chemical Engineers and the Association for Manufacturing Excellence (AME).
Well said by author Allan R. Coletta of a new book The Lean 3P Advantage: A Practitioner’s Guide to the Production Preparation Process. Development of the 3P process is attributed to Chichiro Nakao, a former Toyota group manager and the founder of Shingijutsu company. The accepted meaning of 3P is Production, Preparation, Process. Allan is a chemical engineer with an extensive background in manufacturing operations, supply chain and engineering, gained while working in the chemical process and healthcare diagnostics industries. Allan is a practitioner more so than an author and I believe you will enjoy that perspective. Toyota delivers product designs on schedule 98% of the time (as stated by @flowchainsensei on twitter). Now, I am not sure how I can confirm this statement except that I believe this source to be accurate and even if Bob was 50% wrong, it would mean Toyota still exceeds the majority. However, after interviewing Allan and reading the book, I can understand and believe that statement. This is an excerpt from the book: Lean 3P is a powerful enabler for invention and innovation because it creates a structure and a process for people to create both independently and collaboratively. However, 3P is not presented as a "one size fits all" means of creating brilliant new products that takes us from "blue sky" to product launch. It might work like that in some instances where a new product is a variation of an established product or in organizations where the same team is inventing, developing, and working together to launch a new product. With additional experience the role of 3P in the full product development will likely expand. For companies new to Lean 3P, the question might be how 3P will integrate into existing product development processes. A recent blog post, Applying Lean in the Lean 3P Design Process contains a written excerpt from the podcast. I talked to Allan for a rather long time and had to shorten the podcast. I chose to cut his acknowledgments of several people that include Andy Johnson, Maria Stopher, Ken Rolfes and two former Business901 podcast guests, Drew Locher and Ron Masticelli. I apologize to any that he mentioned and I failed to here. Allan’s Lean experience started while serving as Site Manager for ICI Uniqema’s largest Specialty Chemicals plant in North America and continued to expand is his role as Senior Director of Engineering for Siemens Healthcare Diagnostics. His passion for manufacturing and engaging people in continuous improvement continues to grow through personal application of Lean principles. Allan serves on the Delaware Manufacturing Extension Partnership’s Fiduciary and Advisory Boards, and is a member of the Delaware Business Mentoring Alliance. He is also a member of the American Institute of Chemical Engineers and the Association for Manufacturing Excellence (AME).
Well said by author Allan R. Coletta of a new book The Lean 3P Advantage: A Practitioner’s Guide to the Production Preparation Process. Development of the 3P process is attributed to Chichiro Nakao, a former Toyota group manager and the founder of Shingijutsu company. The accepted meaning of 3P is Production, Preparation, Process. Allan is a chemical engineer with an extensive background in manufacturing operations, supply chain and engineering, gained while working in the chemical process and healthcare diagnostics industries. Allan is a practitioner more so than an author and I believe you will enjoy that perspective. Toyota delivers product designs on schedule 98% of the time (as stated by @flowchainsensei on twitter). Now, I am not sure how I can confirm this statement except that I believe this source to be accurate and even if Bob was 50% wrong, it would mean Toyota still exceeds the majority. However, after interviewing Allan and reading the book, I can understand and believe that statement. This is an excerpt from the book: Lean 3P is a powerful enabler for invention and innovation because it creates a structure and a process for people to create both independently and collaboratively. However, 3P is not presented as a "one size fits all" means of creating brilliant new products that takes us from "blue sky" to product launch. It might work like that in some instances where a new product is a variation of an established product or in organizations where the same team is inventing, developing, and working together to launch a new product. With additional experience the role of 3P in the full product development will likely expand. For companies new to Lean 3P, the question might be how 3P will integrate into existing product development processes. A recent blog post, Applying Lean in the Lean 3P Design Process contains a written excerpt from the podcast. I talked to Allan for a rather long time and had to shorten the podcast. I chose to cut his acknowledgments of several people that include Andy Johnson, Maria Stopher, Ken Rolfes and two former Business901 podcast guests, Drew Locher and Ron Masticelli. I apologize to any that he mentioned and I failed to here. Allan’s Lean experience started while serving as Site Manager for ICI Uniqema’s largest Specialty Chemicals plant in North America and continued to expand is his role as Senior Director of Engineering for Siemens Healthcare Diagnostics. His passion for manufacturing and engaging people in continuous improvement continues to grow through personal application of Lean principles. Allan serves on the Delaware Manufacturing Extension Partnership’s Fiduciary and Advisory Boards, and is a member of the Delaware Business Mentoring Alliance. He is also a member of the American Institute of Chemical Engineers and the Association for Manufacturing Excellence (AME).
In a past Business901 podcast, Software Quality Assurance Podcast with Murali Chemuturi, we discussed Software Quality Assurance and what Murali considers best practice. I found his position quite different from the Agile and Kanban Software people I typically interview. Recently I came across another subject, Measuring Customer Satisfaction, that Murali takes an unique position. This was basis for this podcast. J. Ross Publishing has recently published three books authored by Murali Chemuturi Mastering Software Quality Assurance: Best Practices, Tools and Techniques for Software Developers Mastering Software Project Management: Best Practices, Tools and Techniques Software Estimation Best Practices, Tools & Techniques: A Complete Guide for Software Project Estimators
In a past Business901 podcast, Software Quality Assurance Podcast with Murali Chemuturi, we discussed Software Quality Assurance and what Murali considers best practice. I found his position quite different from the Agile and Kanban Software people I typically interview. Recently I came across another subject, Measuring Customer Satisfaction, that Murali takes an unique position. This was basis for this podcast. J. Ross Publishing has recently published three books authored by Murali Chemuturi Mastering Software Quality Assurance: Best Practices, Tools and Techniques for Software Developers Mastering Software Project Management: Best Practices, Tools and Techniques Software Estimation Best Practices, Tools & Techniques: A Complete Guide for Software Project Estimators
In a past Business901 podcast, Software Quality Assurance Podcast with Murali Chemuturi, we discussed Software Quality Assurance and what Murali considers best practice. I found his position quite different from the Agile and Kanban Software people I typically interview. Recently I came across another subject, Measuring Customer Satisfaction, that Murali takes an unique position. This was basis for this podcast. J. Ross Publishing has recently published three books authored by Murali Chemuturi Mastering Software Quality Assurance: Best Practices, Tools and Techniques for Software Developers Mastering Software Project Management: Best Practices, Tools and Techniques Software Estimation Best Practices, Tools & Techniques: A Complete Guide for Software Project Estimators
Open Space Technology (OST) is an approach for hosting meetings, conferences, corporate-style retreats, symposium, and community summit events, focused on a specific and important purpose or task—but beginning without any formal agenda, beyond the overall purpose or theme. I have become quite intrigued by this method and was first introduced to the concept several years ago by Jim Benson, co-author of Personal Kanban. You can even try it out by holding a Lean Coffee session of your own: What is a Lean Coffee? Essentially, a Lean Coffee is a group of people working together to learn about lean in an informal setting. It's like a mini-unconference where the participants decide on the schedule. The timeframe is typically one to two hours. The number of people is best between 6-8 but 4-10 works fine. One person facilitates these actions:. Everybody writes down topics they'd like to discuss on stickies placing them in a column in the center of the table. Give as much time as needed, but typically takes only 3-5 minutes. Each topic is briefly described by its writer (15-30 seconds typically per stickie). Each person gets three votes which they indicate by marking the voted for stickie with a dot (they can put as many votes as they like on one stickie). The top three stickies are placed in a new column, ordered by the stickies with the most votes at the top Each of these stickies are discussed for 5-15 minutes. When the facilitator thinks the discussion has reached a good end-point she asks if everyone is complete. When complete move the stickie over into a new column that represents 'done'. Repeat step until all done. If enough time is left over, do another stickie or two. Celebrate being done. Lean Coffee Template on Google Docs When is the last time you went to a conference and came away thinking the coffee breaks were the best part of it. The LSSC 2012 - Lean Systems Society conference this year held a day long Lean Camp before the 3-day conference which followed this open space type thinking. They also held the Lean Coffee sessions each morning of the conference. The only problem with doing that is that it made it extremely difficult to attend the morning keynote. The Lean Coffee was that engaging, and they never used my topic either. In this podcast, John Steinbach follows up from yesterday’s podcast, Opening Appreciative Space Process 1 and his approaches with more discussion on the Open Space concepts.The process starts with Appreciative Inquiry; a positive approach to change that can be used by individuals, teams, organizations, and communities. Both of these podcast serve as great introduction to this ever-growing concept. Coffee anyone?
Open Space Technology (OST) is an approach for hosting meetings, conferences, corporate-style retreats, symposium, and community summit events, focused on a specific and important purpose or task—but beginning without any formal agenda, beyond the overall purpose or theme. I have become quite intrigued by this method and was first introduced to the concept several years ago by Jim Benson, co-author of Personal Kanban. You can even try it out by holding a Lean Coffee session of your own: What is a Lean Coffee? Essentially, a Lean Coffee is a group of people working together to learn about lean in an informal setting. It's like a mini-unconference where the participants decide on the schedule. The timeframe is typically one to two hours. The number of people is best between 6-8 but 4-10 works fine. One person facilitates these actions:. Everybody writes down topics they'd like to discuss on stickies placing them in a column in the center of the table. Give as much time as needed, but typically takes only 3-5 minutes. Each topic is briefly described by its writer (15-30 seconds typically per stickie). Each person gets three votes which they indicate by marking the voted for stickie with a dot (they can put as many votes as they like on one stickie). The top three stickies are placed in a new column, ordered by the stickies with the most votes at the top Each of these stickies are discussed for 5-15 minutes. When the facilitator thinks the discussion has reached a good end-point she asks if everyone is complete. When complete move the stickie over into a new column that represents 'done'. Repeat step until all done. If enough time is left over, do another stickie or two. Celebrate being done. Lean Coffee Template on Google Docs When is the last time you went to a conference and came away thinking the coffee breaks were the best part of it. The LSSC 2012 - Lean Systems Society conference this year held a day long Lean Camp before the 3-day conference which followed this open space type thinking. They also held the Lean Coffee sessions each morning of the conference. The only problem with doing that is that it made it extremely difficult to attend the morning keynote. The Lean Coffee was that engaging, and they never used my topic either. In this podcast, John Steinbach follows up from yesterday’s podcast, Opening Appreciative Space Process 1 and his approaches with more discussion on the Open Space concepts.The process starts with Appreciative Inquiry; a positive approach to change that can be used by individuals, teams, organizations, and communities. Both of these podcast serve as great introduction to this ever-growing concept. Coffee anyone?
Open Space Technology (OST) is an approach for hosting meetings, conferences, corporate-style retreats, symposium, and community summit events, focused on a specific and important purpose or task—but beginning without any formal agenda, beyond the overall purpose or theme. I have become quite intrigued by this method and was first introduced to the concept several years ago by Jim Benson, co-author of Personal Kanban. You can even try it out by holding a Lean Coffee session of your own: What is a Lean Coffee? Essentially, a Lean Coffee is a group of people working together to learn about lean in an informal setting. It's like a mini-unconference where the participants decide on the schedule. The timeframe is typically one to two hours. The number of people is best between 6-8 but 4-10 works fine. One person facilitates these actions:. Everybody writes down topics they'd like to discuss on stickies placing them in a column in the center of the table. Give as much time as needed, but typically takes only 3-5 minutes. Each topic is briefly described by its writer (15-30 seconds typically per stickie). Each person gets three votes which they indicate by marking the voted for stickie with a dot (they can put as many votes as they like on one stickie). The top three stickies are placed in a new column, ordered by the stickies with the most votes at the top Each of these stickies are discussed for 5-15 minutes. When the facilitator thinks the discussion has reached a good end-point she asks if everyone is complete. When complete move the stickie over into a new column that represents 'done'. Repeat step until all done. If enough time is left over, do another stickie or two. Celebrate being done. Lean Coffee Template on Google Docs When is the last time you went to a conference and came away thinking the coffee breaks were the best part of it. The LSSC 2012 - Lean Systems Society conference this year held a day long Lean Camp before the 3-day conference which followed this open space type thinking. They also held the Lean Coffee sessions each morning of the conference. The only problem with doing that is that it made it extremely difficult to attend the morning keynote. The Lean Coffee was that engaging, and they never used my topic either. In this podcast, John Steinbach follows up from yesterday’s podcast, Opening Appreciative Space Process 1 and his approaches with more discussion on the Open Space concepts.The process starts with Appreciative Inquiry; a positive approach to change that can be used by individuals, teams, organizations, and communities. Both of these podcast serve as great introduction to this ever-growing concept. Coffee anyone?
The energy and creative generated in the Appreciative Inquiry process is shapes the interaction in a dynamic Open Space session where participants generate the agenda for a series of working sessions where concrete actions are identified. This process has been used with small groups to organizations with thousands of members. This is part 1 of the 2-part podcast.John Steinbach has combined the approaches of Appreciative Inquiry and Open Space into his dynamic and positive Opening Appreciative Space process .This process starts with Appreciative Inquiry; a positive approach to change that can be used by individuals, teams, organizations, and communities. Through an interview process that focuses on strengths and high-point experiences, Appreciative Inquiry helps participants discover and create a desired future. This dynamic and uplifting process has been used by Fortune 500 companies, educational institutions, not-for-profit organizations, youth groups, world leaders, and communities. John Steinbach has worked to Open Appreciative Space in a wide variety of organizations including GTE, Verizon, Hughes Electronics, Nationwide Insurance, Boeing, Raytheon, GE, Cardinal Health Systems, United Way, American Red Cross, Purdue Extensions services and dozens of non-profits, churches and youth-serving organizations. John's Website is http://www.jpconsultantsinc.com.
The energy and creative generated in the Appreciative Inquiry process is shapes the interaction in a dynamic Open Space session where participants generate the agenda for a series of working sessions where concrete actions are identified. This process has been used with small groups to organizations with thousands of members. This is part 1 of the 2-part podcast.John Steinbach has combined the approaches of Appreciative Inquiry and Open Space into his dynamic and positive Opening Appreciative Space process .This process starts with Appreciative Inquiry; a positive approach to change that can be used by individuals, teams, organizations, and communities. Through an interview process that focuses on strengths and high-point experiences, Appreciative Inquiry helps participants discover and create a desired future. This dynamic and uplifting process has been used by Fortune 500 companies, educational institutions, not-for-profit organizations, youth groups, world leaders, and communities. John Steinbach has worked to Open Appreciative Space in a wide variety of organizations including GTE, Verizon, Hughes Electronics, Nationwide Insurance, Boeing, Raytheon, GE, Cardinal Health Systems, United Way, American Red Cross, Purdue Extensions services and dozens of non-profits, churches and youth-serving organizations. John's Website is http://www.jpconsultantsinc.com.
The energy and creative generated in the Appreciative Inquiry process is shapes the interaction in a dynamic Open Space session where participants generate the agenda for a series of working sessions where concrete actions are identified. This process has been used with small groups to organizations with thousands of members. This is part 1 of the 2-part podcast. John Steinbach has combined the approaches of Appreciative Inquiry and Open Space into his dynamic and positive Opening Appreciative Space process .This process starts with Appreciative Inquiry; a positive approach to change that can be used by individuals, teams, organizations, and communities. Through an interview process that focuses on strengths and high-point experiences, Appreciative Inquiry helps participants discover and create a desired future. This dynamic and uplifting process has been used by Fortune 500 companies, educational institutions, not-for-profit organizations, youth groups, world leaders, and communities. John Steinbach has worked to Open Appreciative Space in a wide variety of organizations including GTE, Verizon, Hughes Electronics, Nationwide Insurance, Boeing, Raytheon, GE, Cardinal Health Systems, United Way, American Red Cross, Purdue Extensions services and dozens of non-profits, churches and youth-serving organizations. John's Website is http://www.jpconsultantsinc.com.